在当前全球环境对节能减排的迫切要求下,国家对汽车油耗政策步步收紧,轻量化造车成为实现节能降耗的必经之路。在追求轻量化的同时,我们应注意到,关系到驾乘者生命安全的车辆安全问题具有和节能减排同样重要的意义。为符合日趋严苛的车辆碰撞测试和安全的要求,如何在实现轻量化的同时保证车身强度,成为全球汽车制造商首要考虑的核心要素。而通常,造车工程师们主要从车身材料、车辆结构和连接工艺三方面的优化和平衡配置,来实现车辆“减重”和“增强”的并驾齐驱。
几天前,笔者的一篇《从奥迪A8“逆势增重”看汽车轻量化设计》以全新奥迪A8的车身材料优化配置为例从车辆材料设计视角对当前轻量化技术进行了分析。除了完美的多种车身材料“混搭式”设计,新一代奥迪A8的车身连接方式更是达到了14种,成为极具技术含金量的一大看点。在本篇文章中,我们将继续探究全新奥迪A8先进的车身连接工艺,同时也看看造车界的大佬们,为实现车辆的“减重增强”,在车身连接工艺上使用了哪些吸睛的技能。
接受多材质考验的车身连接技术
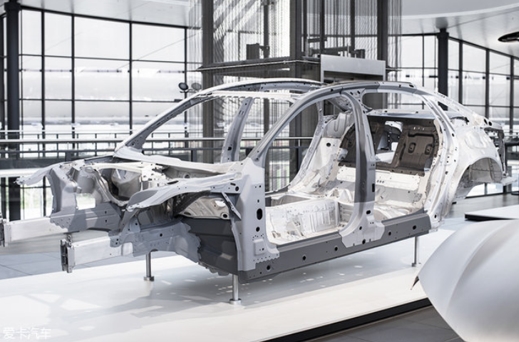
全新奥迪A8的车身结构分别采用了铝、钢、镁以及CFRP碳纤维高分子复合材料四种材料,按种类再细分,材料种类达到29种,包括16种铝材、11种钢材、1种镁材和1种碳纤维复合材料,不同的钢材和铝材都有各自不同的特性。比如铝合金材料对热敏感,采用传统焊接工艺会导致材料强度下降,而且受热易变形,会导致车身材料的拼合尺寸精度很难控制。如何将这些不同特性的材料坚固的连接在一起,解决好不同材料间的连接工艺是关键。
在这一点上,奥迪的工程师颇费心思,参考自家旗舰跑车奥迪R8的多种车身材质拼接技术,在全新奥迪A8上大量应用了自切削螺钉联接、激光焊接、铆接等技术,采用的连接工艺远领先于同行业,车身连接工艺达到14种,包括MIG焊、点焊、保护焊、远程激光焊等8种热连接技术和专门针对铝材的冲铆连接、用于不同材料拼接的自攻螺栓、卷边连接等6种冷连接技术。
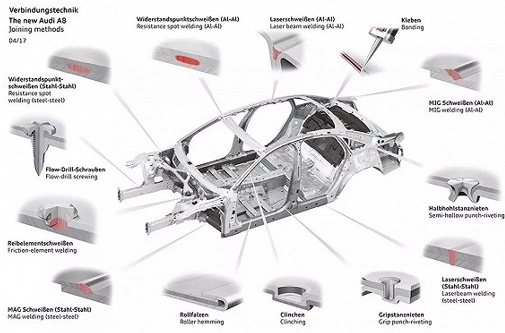
全新奥迪A8的B柱部位材料连接采用了卷边连接和粘合剂连接的封边技术。同时,由于不同材质间热胀冷缩程度的差异,还采用Piece-locking连接技术在卷边处间隔固定距离打上凹坑,使三层材料全部贴合。此外,在车辆的A柱、C柱和车顶位置,也采用了相同的连接方式,这些冷连接工艺将不同材质有效地固定在一起。
车身结构部位的铝合金板材、热成型超高强度钢和普通钢通过卷边连接方式贴合在一起。同时使用粘合剂连接和铆钉连接以确保连接紧固。顶盖和侧围部位采用了远程激光焊接工艺,在焊接过程中,激光头与焊接件的距离将保持在20cm,焊缝更加细腻精准,焊接边缘留出面积可减少27%,激光束的高速率和低能耗也降低了二氧化碳的排放。得益于铝材质量以及铆接技术的发展,车架上的铝型材与新式钢材很好的接合,形成全新奥迪多材料车身结构。
特斯拉领先的全铝车身焊接工艺
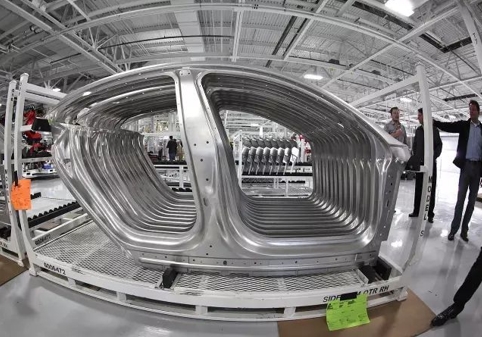
除了全新奥迪A8,大规模使用铝制架构的车还有特斯拉、凯迪拉克和奇瑞捷豹路虎等车型。特斯拉研发制造的Model
S全铝车身具有轻量化与高强度特性,其车身和前后悬架大部分材料均采用了铝材,焊接工艺主要使用了CMT(Cold metal
Transfer)冷金属过渡技术及Delta Spot电阻点焊技术,克服了铝合金材料遇热易变型的难题。
CMT冷金属过渡技术由奥地利伏能士焊接技术公司在2005年推出,能焊接厚度为0.3mm的超轻板材。和传统的MIG/MAG焊接相比,真正实现了“冷过渡”。由于对焊缝的持续热量输出时间极短,可给焊缝一个冷却过程,显著降低了薄板焊接变形量,使焊缝形成良好的搭桥能力,降低了工件的装配间隙要求及对夹具精度的要求。同时,CMT电弧极其稳定,电弧长度可被机械的检测和调整,无论工件表面以何种速度焊接,电弧始终保持稳定,焊接过程几乎无飞溅及烧穿现象。
Delta
Spot电阻点焊技术是伏能士针对铝焊研发的新技术,其创新点在于电极带的发明。由于母材和电极受到电极带保护,电极带在电极和需要接合的母材之间运动进而实现连续的焊接,可确保在多个班制中保持恒定的质量水平,具有高度的工艺可靠性。“两厚一薄”的三板连接由于焊点在厚板范围内形成难以抓住薄板,因此对于传统电焊来说是个老大难问题。而Delta
Spot的电极带通过其额外的热输入能针对性地控制焊点的深度,薄板范围中的低热量可通过电极带利用高电阻来弥补,焊点可充分深入薄板,从而能精确控制热输入量。
除了应用于铝焊,Delta Spot技术还可应用于多种材料的焊接,比如高强钢、表面镀层材料、铝、不锈钢、钛、镁、复合材料等,对不同的材料种类和不同厚度,该技术都有出色的表现,如高标准的焊点外观及表面镀层的高强钢材料焊接等。
航空级车身铆接胶合技术

和传统钢制车身不同,由于白车身大面积应用铝合金,不同材料间差异化的物理属性导致用常规的焊接技术难以实现有效连接,因此,奇瑞捷豹路虎引入了一项世界级工艺——航空级车身铆接胶合技术,这一技术不但解决了铝合金连接的难题,很大程度也提升车身强度。
该技术由伺服电机提供动力将铆钉直接压入待铆接板材,在铆钉的压力下铆钉板材和铆钉发生塑性形变,充盈于铆模之中,该技术制造的车身拥有强大的抗疲劳度、静态紧固力和防撞击能力,有效解决了铝合金连接的难题,车身也更坚固。
由于铝材和钢材具有不同的金属电位,需在铆接部位填充粘合剂。通过可视化涂胶监测系统,能实时监测粘合剂的长度、直径、轨迹等关键工艺参数,确保粘合剂填充位置的精准。使用粘合剂也将车身连接强度增至单纯铆接强度的2-3倍。
降本增效的“钢铝”车身连接工艺
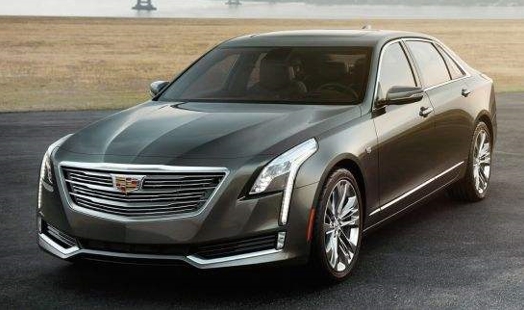
在汽车制造商纷纷开发全铝车型的同时,通用另辟蹊径,推出豪华轿车凯迪拉克CT6“钢铝”车身。和全铝车身相比,“钢铝”车身可节省大量的时间和经济成本,将传统钢制车身的生产线转换为钢铝焊接生产线所耗费的成本也要远远低于实现全铝制技术所花费的成本,比如福特为将其钢制车身F-150打造为全铝制车身,将位于密歇根州的德尔伯恩市的生产线拆除建造了全新生产线,此项工程花费了数百万美元和数月时间。而实现“钢铝”技术的最大困难在于,由于钢和铝两种金属的熔点不同,在钢刚开始加热的时候,铝就已经融化,这让绝大多数汽车制造商望而却步。
通用在设计凯迪拉克CT6前对钢铝焊接工艺进行了大量的研究,研发出一种新型的焊接工艺,在凯迪拉克CT6前引擎盖和汽车尾部进行钢铝焊接,将钢和铝牢固焊接在一起,打造出全新“钢铝”车身。目前通用的焊装车间可以采用铝电阻点焊、铝激光钎焊、自攻螺接、自冲铆接四种工艺实现钢铝连接,其中铝电阻点焊可以解决铝材的氧化层问题。
采用新型焊接工艺的“钢铝”车身整备质量轻速度快,制造成本也相对较低,在降低油耗的同时,车辆性能也大幅提升。
“减重增强”是汽车产业发展的必然趋势,汽车轻量化材料的发展永无止境,车身连接技术及工艺也将因此不断优化和革新。汽车制造商们亮出“十八般武艺”,以技术创新推动着世界汽车工业的发展,谁能笑到最后?不妨让我们拭目以待。